Boat Construction and Repair
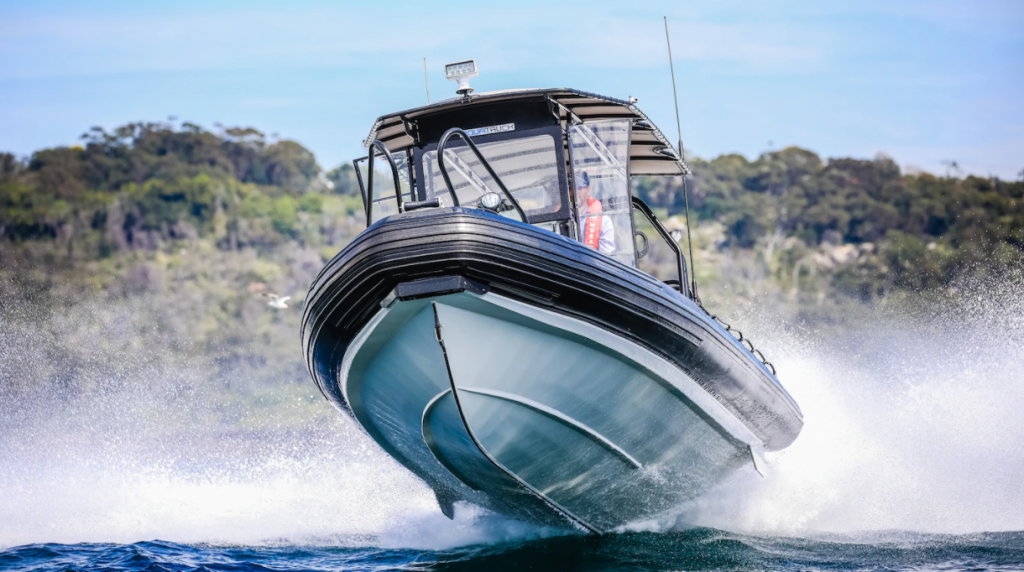
HDPE Boats
This makes HDPE boats nearly maintenance-free. Unlike other boat materials, this material is also environmentally friendly and cost-efficient. Furthermore, it absorbs vibrations, making for a better and more enjoyable experience for passengers.

These plastic boats are mostly produced for customers in the commercial sector who use them for lifeboats/workboats in the fishing industry, as well as police and military use (personal security, coastal region water security, etc.).
Leister’s hand-held extruders and heat guns are the ideal tools to produce HDPE boats.
Welding Inflatable Boats
Inflatable boats, sometimes referred to as rubber dinghies, have an inflatable tube for a hull. They are produced from plastic film, mainly PVC or synthetic rubber, such as PU.
Storing these boats is made easy thanks to their valve, which lets the air out.
In addition to the classic inflatable boat made for two people to paddle on a lake, there are other variants, such as inflatable kayaks and rafts. Last but not least, there are lifeboats used for ships and airplanes.
Inflatable boats can be welded with hot air and sealed with tape to ensure complete watertightness and a long life-span. These 3D forms can be constructed using Leister’s welding machines. Heat guns make repairs easy as well.
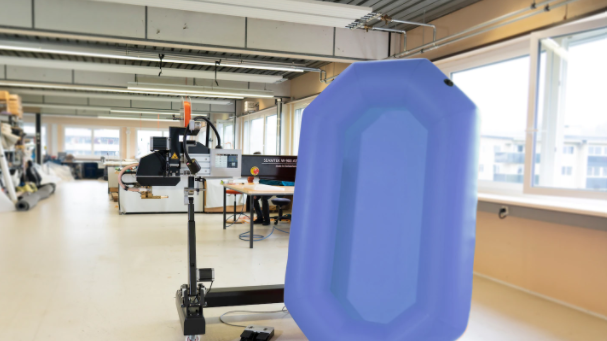
Peel test: Flame vs. BITUMAT
Various tanks made from hard plastics or flexible membrane materials are used on all kinds of boats. These include freshwater tanks for drinking water, wastewater tanks and ballast water tanks for speedboats, such as those used for wakeboarding. Tanks that are made from food-safe polypropylene or tarpaulins, depending on their intended application, have an advantage over flexible containers since they can be firmly anchored in place, thus preventing any shifting.
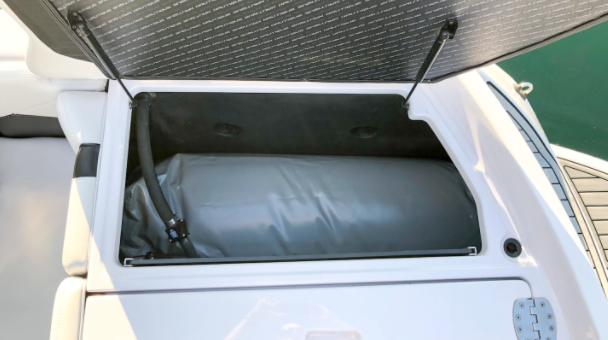
Most of them have an opening large enough for ventilation, filling and draining with a gas-tight seal. Other advantages include their longer life-span and greater stability, making them more environmentally friendly. The sanitary tanks can also be used in campers, vans or motorhomes and can be installed by both professionals and those with less experience. The hard, plastic tanks are primarily manufactured and repaired with extruders. Tanks that are made from flexible material are joined together with tape using welding machines, i.e. glued or otherwise welded and thus made watertight.